Facility Maintenance
Building Your Facility Management Program
Did You Know there is a 4 minute educational video on Onboarding FM Vendors? Did You Know there is a 4 minute educational video on Developing SLA’s for Your FM Program?
Click below and explore our entire Did You Know series on facility maintenance programs where we explore topics including but not limited to Best Practices of Triaging a Work Order, Developing SLAs and Why Hourly Rates Lie.
Playlist
Request a copy of our Sustainability Fact Sheet for Facility Maintenance and explore some of the most innovative sustainability solutions for Facility Maintenance today.
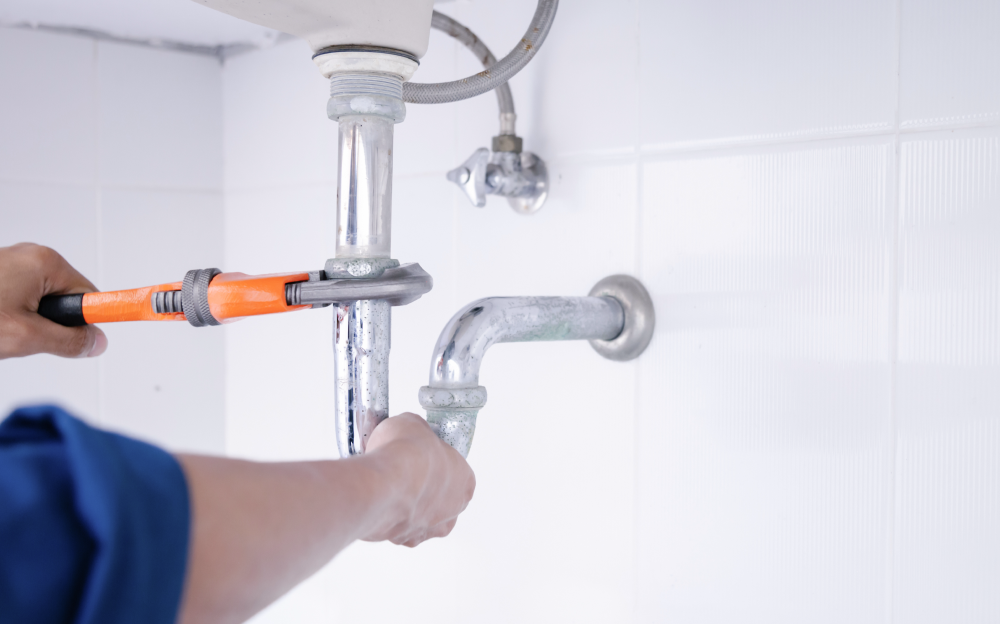
Our Approach
Ferrandino & Son’s value proposition for companies pursuing a better facility maintenance program is improved efficiency. Leveraging AI technology to automate our administrative processes allows our teams to create a more enhanced triage process, driving down our average cost-per-ticket across all of our service trades.
Vendor dispatches happen in real-time, effectively providing a near zero-delay response for priority service requests. Discover how a fully-integrated facility solution can provide a more cost-effective solution for your portfolio.
Services: Break Fix
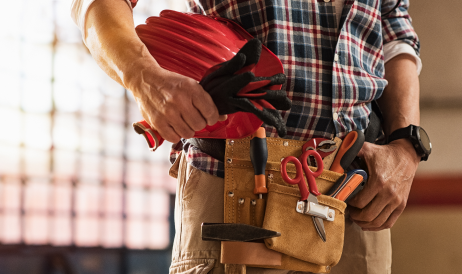
Handyman
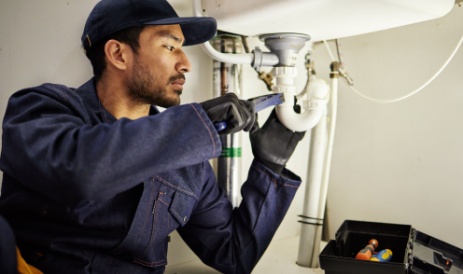
Plumbing
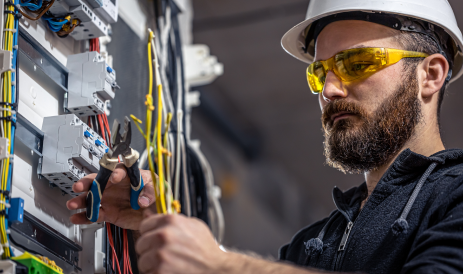
Electrical
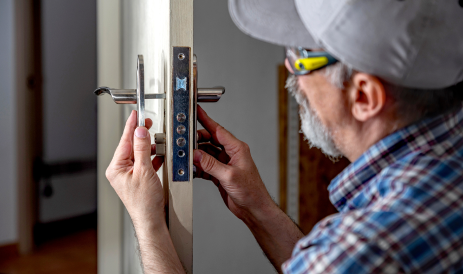
Doors
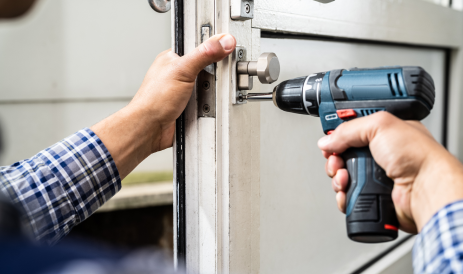
Locks
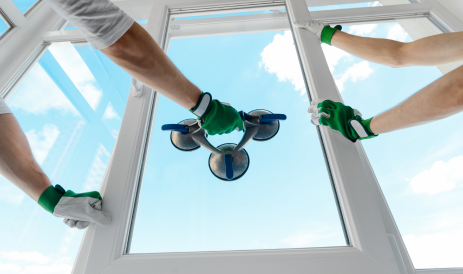
Our Technology Integrations
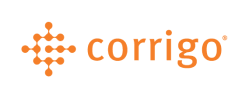
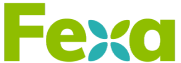
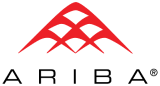
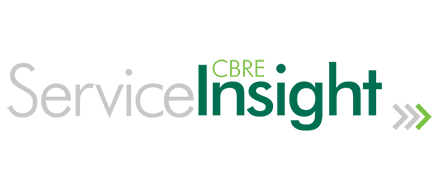
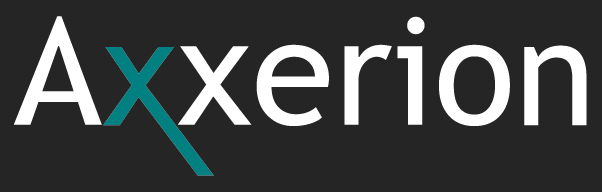
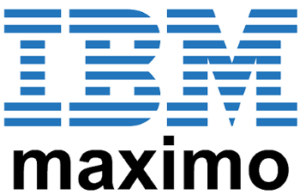

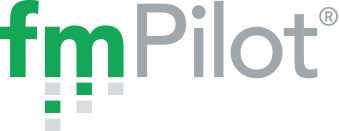
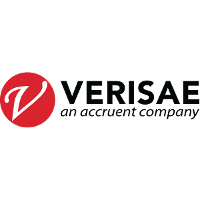
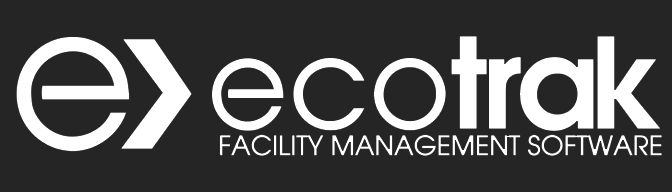
Our Workflow Process
Work Order Dispatched by Client
Auto-Acceptance-Loaded into our work order system
↓
Prioritized with SLA
↓
Assigned to Procurement
Scope of Work Confirmation
Reach out to Originator
↓
Review Scope of Work
↓
Triage Possible Quick Fix
Accept or Decline Work Order
Confirm Assigned to Specific Scope
↓
Review Scope Against Priority
↓
Confirm Ability to Deliver
Procure and Assign Technician
Vet Scope Against Technician Capabilities
↓
Review Scope of Work
↓
Discuss Possible Equipment and Material Needed
Dispatch Technician
Review Security Protocols
↓
Reconfirm Scope of Work
↓
Update Notes in Work Order Platform
Monitor Technician on-site
Review Initial Troubleshooting
↓
Partner on a Possible Solution
↓
Work to Resolve During this Visit
Confirm Service Complete
Review Results of the Repair
↓
Review Scope of Work Again
↓
Have Technician Confirm Satisfaction with On-Site Manager
Follow Up with Store on Completed Services
Confirm Actual Repair
↓
Ensure Satisfaction
↓
Document and Close in Work Order Platform
Invoice Client and Pay Technician
Dedicated Client Billing Team
↓
Automated Vendor Payment
↓
Final Close Out in Our System
Program Elements
Cost Savings
- Understanding SLA and Cost per Ticket
- Triage Process identifies any gaps in service before technician is dispatched
- Reducing Cost per Ticket through program improvements
Material Purchasing
- Purchasing Strategy
- Needed Materials
- Good, Better & Best Solutions
- Buildout Material List
-  What’s Needed
- Opportunities for Savings
- Confirm Warranties
- Develop Timeline
- Acquisition & Schedules
Scorecarding Vendors
- Ferrandino & Son procurement process
- Key attributes of a provider
- Vendor Rating and Review
- Managing vendor KPI’s
Proposal Review
- Service crossover
- Competitive Advantage – Managing Cost through previous vendor relationships
- Acquisition of parts – strategic sourcing
- Maximum volume management
- Flexibility and integration in work order systems
Safety Requirements
- Identify themselves by uniform and ID
- Required to follow state/local and OSHA guidelines including the use of Personal Protective Equipment
- Follow all documented safety protocols when on site
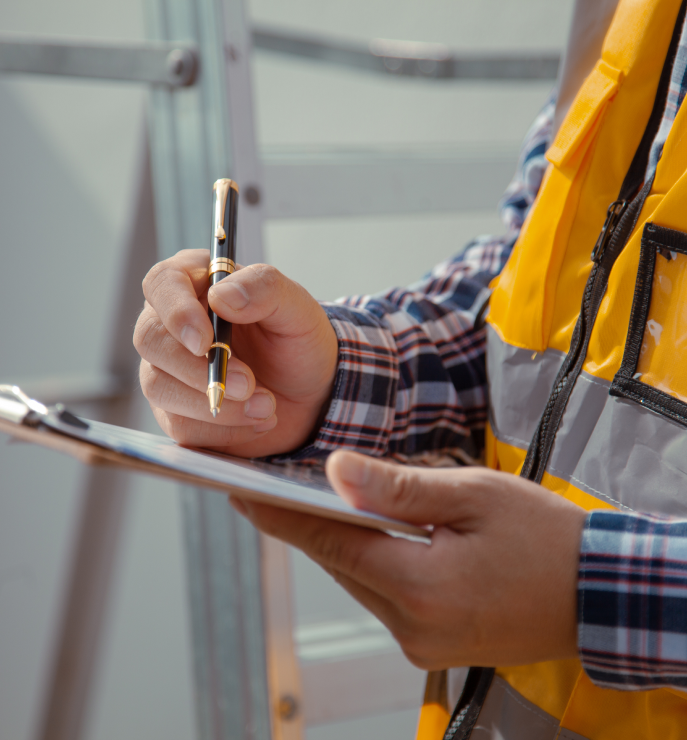
Considering Ferrandino & Son as a facility partner? 
Click the button to request a rate card.
Looking for Personalized Answers for your Portfolio? Talk to our Subject Matter Experts on a wide range of Facility Maintenance topics!